How is OEE calculated?
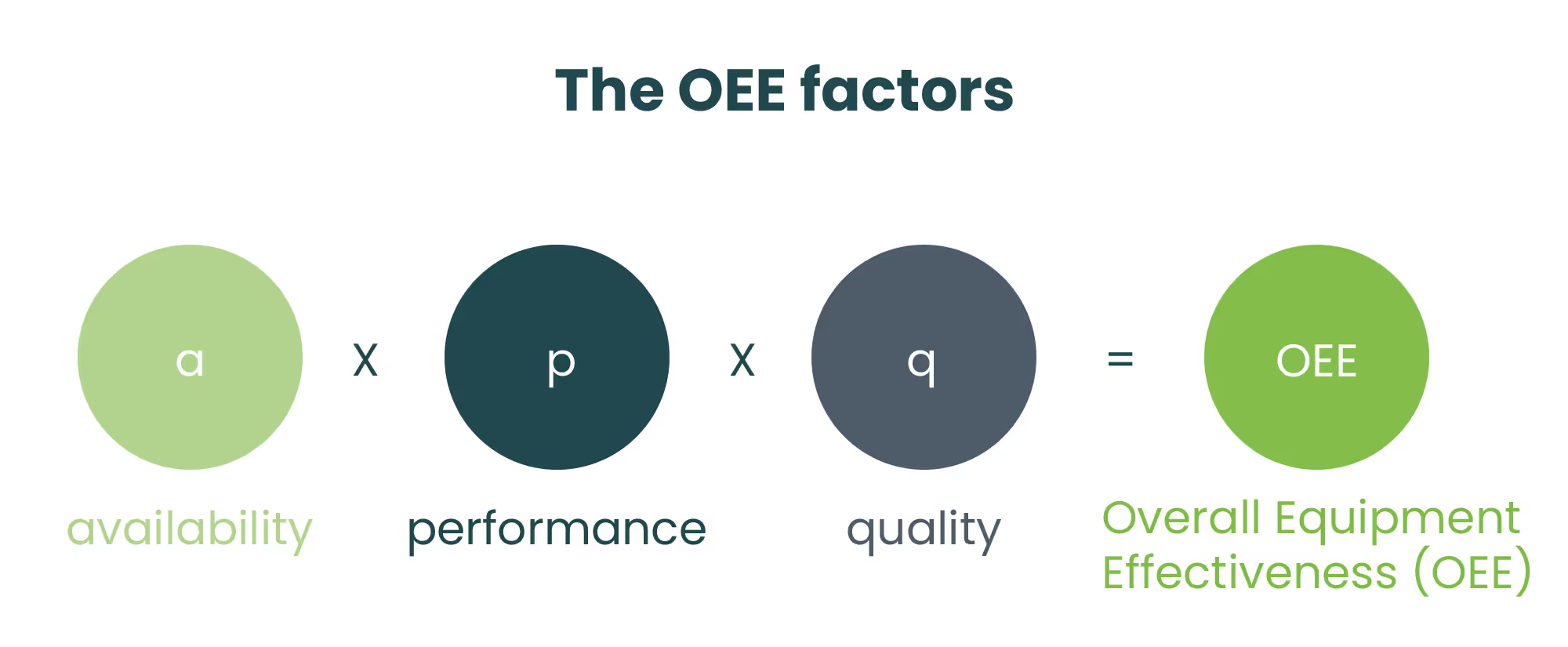
OEE is calculated by multiplying availability, power efficiency, and quality factor. The availability factor measures the operating time of the plant in relation to the planned operating time. The power efficiency compares the actual performance with the maximum possible output and the quality factor takes into account the proportion of defect-free products.
Availability factor: The availability factor measures the operating time of a plant in relation to the planned production time. Plant failures and set-up times impair this factor. A high percentage means continuous production.
Power factor: The power factor takes into account the effective running time compared to the maximum possible running time. Small stops and reduced speeds can affect performance. A high value indicates efficient use of the system.
Quality factor: The quality factor looks at the quality of the parts produced. Scrap and reworked parts reduce this value, and process errors and previous issues can affect quality. A high percentage, on the other hand, indicates error-free production.
An OEE of 100% means optimal plant utilization, maximum output and error-free production. The continuous monitoring and optimization of these dimensions is crucial for the efficiency of production processes.