4 types of maintenance measures
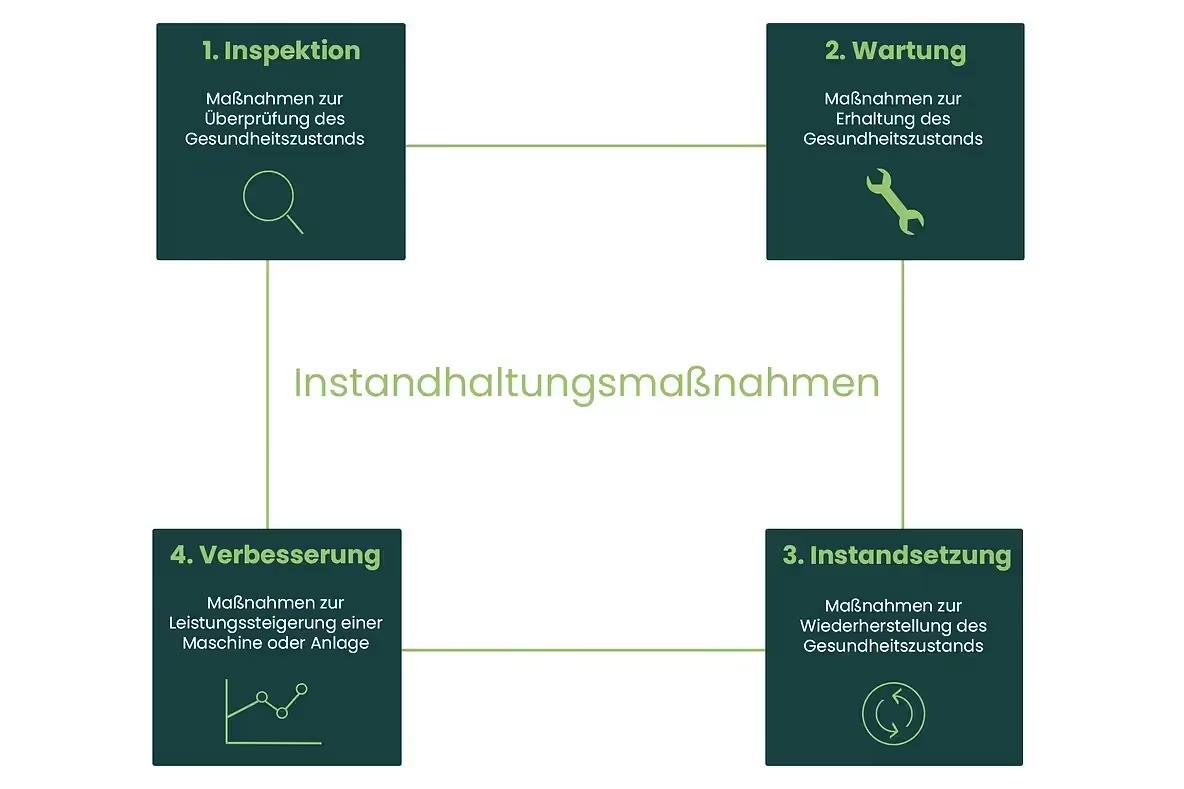
1st inspection: Regular inspection of the machine's health status, e.g. visual checks and functional tests, in order to identify wear or damage at an early stage. One example is testing manufacturing robots for mechanical wear and malfunctions.
2. Maintenance: Planned measures to maintain health, such as cleaning, lubrication and replacement of wear parts. One example is the regular replacement of hydraulic filters in production machines to maintain their efficiency.
3. Repair: Repairs to restore health/functionality following a defect. For example, replacing a faulty transmission in a production machine.
4. Improvement: Measures to increase efficiency or safety, such as retrofitting machines with modern sensors for better monitoring. For example, installing vibration sensors to become aware of storage problems at an early stage.